The growing demand for renewable energy has led to a surge in solar panel manufacturing, as solar energy emerges as one of the most efficient and sustainable solutions to the world’s energy needs. Behind the simplicity of solar panels lies a sophisticated and meticulous manufacturing process that transforms raw materials into advanced, energy-generating products. In this blog, we’ll take an in-depth look at how solar panels are made, covering each critical step in the factory production line, from raw solar cells to the final product.
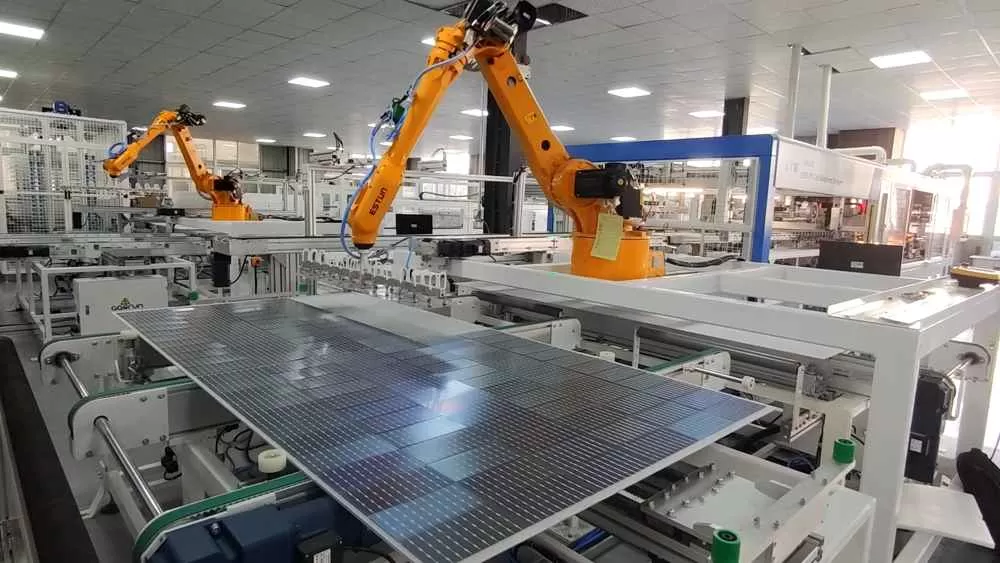
Understanding Solar Panels: The Basics
Solar panels are composed of photovoltaic (PV) cells, which capture sunlight and convert it into electricity. These panels are made from materials that conduct electricity when exposed to sunlight, usually silicon-based cells, which are layered with protective materials.
Modern solar panels are highly efficient, reliable, and designed to last for decades, making them a key component in the global shift towards renewable energy.
Now, let’s explore how solar panels are manufactured, step by step.
Step 1: Procuring the Core Components
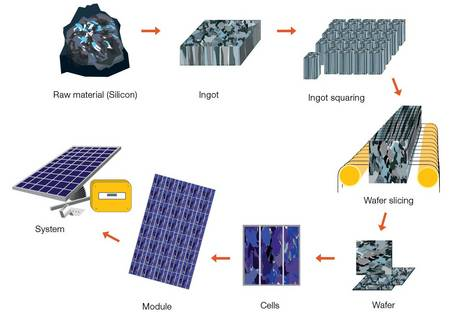
The journey begins with gathering the essential raw materials. The main components of solar panels include:
Each of these components undergoes rigorous quality control checks before entering the production line. Defective materials are immediately discarded to ensure the panel’s long-term efficiency and durability.
Step 2: Cutting and Preparing the EVA and Glass
In the first stage of manufacturing, EVA sheets are cut to precise sizes, much like how a tailor cuts fabric. This is an automated process, ensuring the dimensions match the panel’s design specifications. The EVA sheets will act as a cushion between the solar cells and the tempered glass.
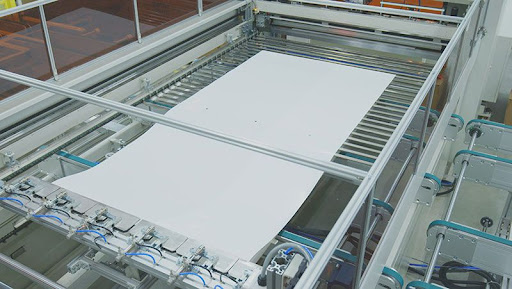
The tempered glass is also prepared at this stage. This glass must be 100% clean and free of imperfections to ensure the highest efficiency of sunlight absorption.
Automated machines handle the glass to prevent contamination, such as fingerprints or dust particles, which could reduce the panel’s effectiveness.
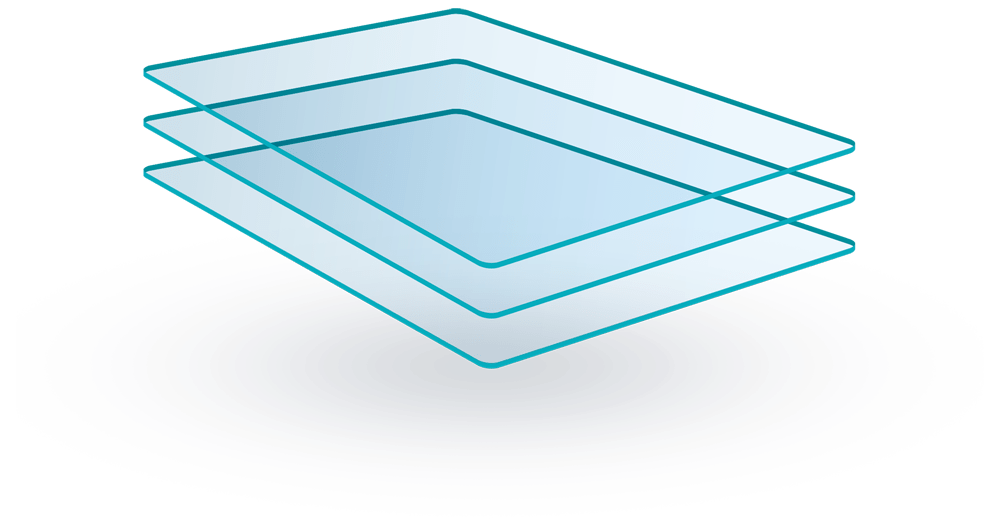
Step 3: Assembling Solar Cells and Creating Strings
Solar cells are the core of the panel, and their arrangement is critical. Factories often use advanced solar cells, such as M10 cells with 10 bus bars. Bus bars are thin strips of conductive material that help carry the electrical current generated by the solar cells. The more bus bars, the more efficient the panel’s energy output, as they reduce the resistance and improve power flow.
The cells are laid out and connected in series to form strings. Each string is aligned with precision, ensuring that the electrical flow between the cells is consistent and free of defects. The soldering process is fully automated, and each connection between the cells is tested to ensure it can withstand high power loads.
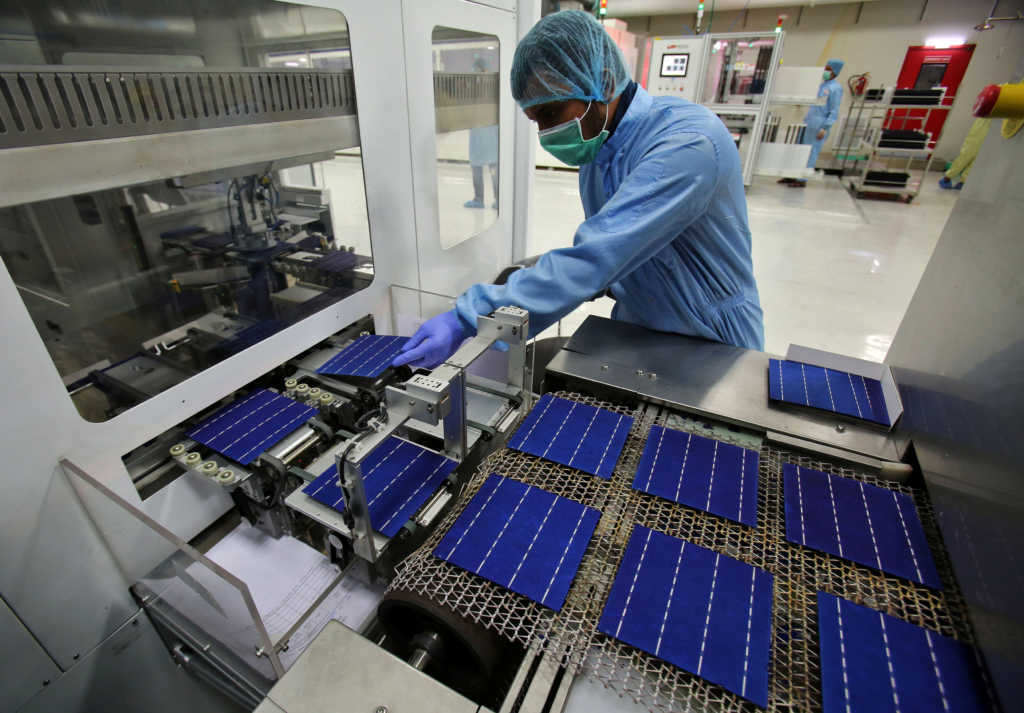
Step 4: Automated Quality Checks
At this point, the partially assembled panels undergo automated quality checks. This is where advanced robots inspect every inch of the panel to detect potential issues, such as:
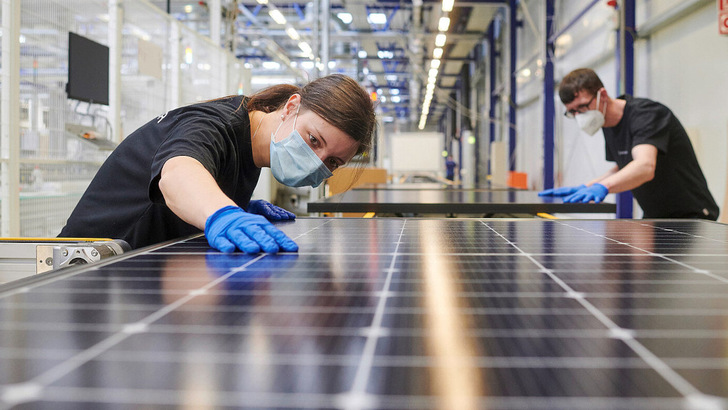
Only panels that pass these stringent tests move forward.
Any defects result in the panel being rejected and either repaired or scrapped.
Step 5: Stringing and Soldering the Cells Together
Once the solar cells are arranged into strings, they are soldered together to create the electrical connections that will power the panel. This process is carried out by highly precise robotic systems, ensuring each connection is secure and durable. Operators monitor the system, but most of the work is automated to guarantee consistency.
This step is crucial, as any errors in the connections can reduce the efficiency of the panel or even cause malfunctions down the line.
Each soldered string is then connected to the junction box, which will eventually link the panel to the external electrical grid or battery storage system.
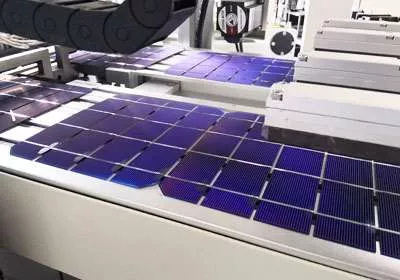
Step 6: Laminating the Panel
Lamination is a critical step that seals the solar cells and other components together into one durable unit. The solar cells, sandwiched between the tempered glass and the back sheet, are encapsulated using the EVA layers. The panel is placed in a laminating machine, where it is heated and pressurised, bonding the layers together into a single, weather-resistant unit.
Before the lamination process is completed, the panel undergoes a Prill Test, a final quality check to ensure there are no defects or misalignments that would affect performance.
Once laminated, the panel is sealed, and ready for long-term outdoor use.
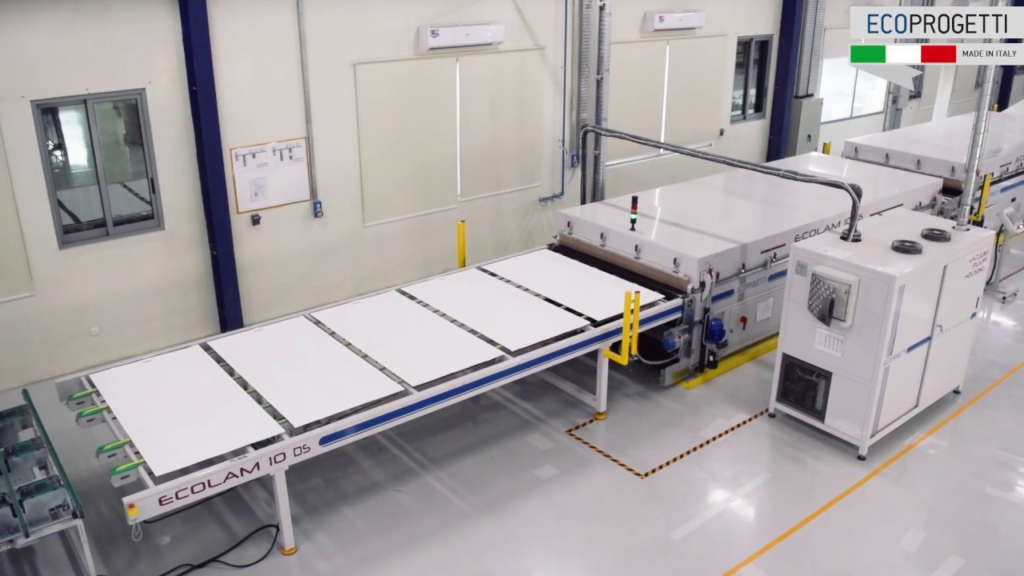
Step 7: Final Quality Inspections
After the lamination process, the panel is subjected to a series of final inspections:
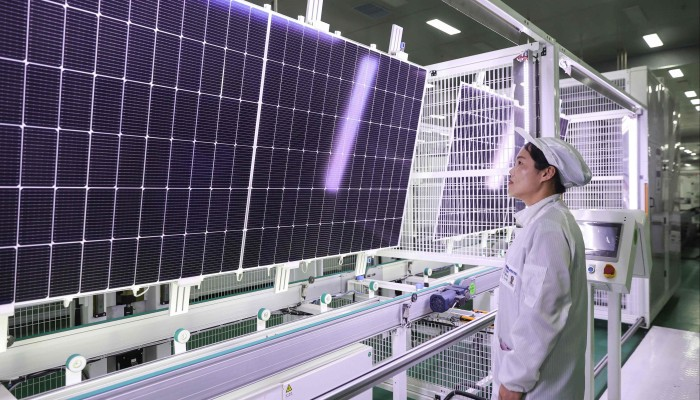
The panels are also tested for their resistance to environmental factors, such as humidity, temperature changes, and UV exposure. These tests confirm that the panel can perform optimally in real-world conditions.
Step 8: Packaging and Dispatch
Once the panels pass all the quality control checks, they are ready for packaging. The panels are carefully packed to prevent any damage during transport.
After packaging, they are dispatched to customers or installation sites, where they will be used to generate clean, renewable energy for homes, businesses, and power grids.
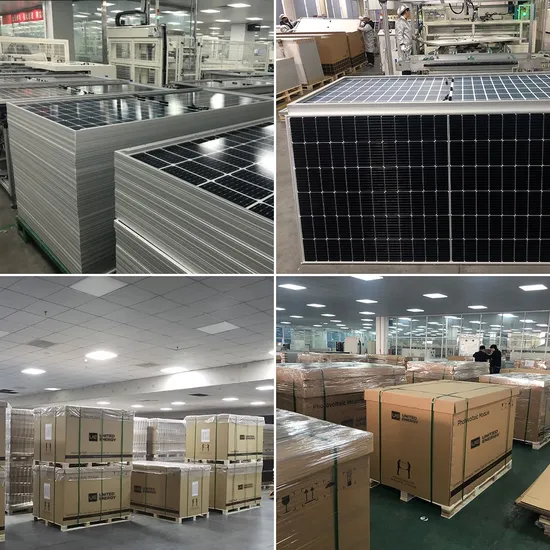
Future of Solar Panel Manufacturing
Solar panel technology is continuously evolving, with factories already preparing for the production of next-generation panels, such as those using M10 and M12 cells. These cells promise even greater efficiency and power output, reducing the number of panels needed to generate the same amount of energy.
Moreover, as automation and artificial intelligence play a larger role in manufacturing, the production process will become faster, more precise, and more cost-effective. This will make solar energy even more accessible to consumers worldwide, accelerating the transition to a cleaner energy future.
Conclusion
The journey of solar panels from raw cells to the final product is a testament to human innovation and the power of automation. Factories use cutting-edge technology and rigorous quality control processes to ensure that each panel performs reliably for decades. As we move towards a more sustainable future, solar panel manufacturing will continue to evolve, driving down costs and improving efficiency.
Solar energy has become an indispensable part of the global energy mix, and with continued advancements in manufacturing, it’s only a matter of time before solar power becomes the primary source of energy worldwide. Stay tuned as the future of solar technology unfolds, and don’t forget—every solar panel manufactured is a step closer to a greener, more sustainable planet.